In the automotive industry, rubber hoses function like "blood vessels," running through engine, fuel, and cooling systems to transport fluids, provide insulation, and absorb vibrations. These hoses must endure high temperatures and pressures while adapting to complex spatial geometries, placing high demands on mold manufacturing.
Learn more about this application case.
Bottlenecks of Traditional Metal Molds: Unable to Meet Both Precision and Customization
Rubber hose molds have traditionally relied on metal materials, produced through multiple steps such as cutting, welding, and thermal forming. In forming environments exceeding 200°C, these molds must maintain dimensional stability. However, faced with modern automotive requirements for lightweighting, customization, and complex geometries, traditional molds reveal multiple shortcomings:
-
High-temperature deformation, difficult precision control: Rubber hoses demand extremely tight tolerances, with inner diameter tolerances within ±0.3 mm. Metal molds are prone to deformation after repeated thermal expansion and contraction, leading to uneven wall thickness or misaligned joints, which severely affect sealing performance.
-
Complex working conditions, limited design freedom: Traditional machining struggles with twisted or irregular geometries, hindering fluid dynamic optimization. Manual processing is time-consuming and error-prone.
-
Long production cycles, high costs: The conventional mold-making process requires coordination across multiple machines and usually takes several weeks from design to delivery—unsuitable for fast, small-batch production.
-
Poor corrosion resistance: Metal molds in contact with fuel, lubricants, and other chemicals are prone to corrosion and rust, reducing their lifespan.
To overcome these challenges, high-performance material molds based on FDM 3D printing technology have emerged as an ideal alternative, enabling flexible manufacturing for the automotive industry.
FUNMAT PRO 610HT + PEI1010: The Perfect Solution for High-Temperature Environments
The INTAMSYS FUNMAT PRO 610HT industrial 3D printer, combined with PEI1010 high-performance engineering plastic, offers a mold-making approach that balances precision, efficiency, and reliability for high-temperature rubber hose forming.
Specifically designed for high-performance materials, the FUNMAT PRO 610HT features an ultra-large build volume of 610 × 508 × 508 mm and industry-leading temperature control: chamber temperatures up to 300°C and nozzle temperatures up to 500°C. This ensures a stable and uniform thermal environment when printing PEI1010, PEEK, PEKK, PPSU, and other advanced thermoplastics, guaranteeing dimensional accuracy and structural integrity.
PEI1010 provides excellent heat resistance (continuous use over 200°C), mechanical strength, and dimensional stability. Compared to metal molds, it is approximately 60% lighter—making it easier to handle and install. Its inherent chemical resistance also protects against corrosion from oil-based media.
Thanks to the FDM process’s ability to print complex geometries as a single piece, designers are no longer constrained by traditional machining paths. Freely designed twisted or curved surfaces help optimize fluid flow and overall performance, significantly reducing design and validation cycles.
Precision and Efficiency – A Comprehensive Breakthrough
-
High-temperature dimensional stability: High accuracy for extreme conditions
PEI1010 maintains excellent dimensional accuracy even above 200°C. Mold critical dimensions such as pipe diameters can consistently stay within ±0.1 mm, ensuring product consistency and reliable sealing. -
Complex geometry, one-piece printing: unleashing design potential
No need for post-assembly—any curvature or complex surface can be directly manufactured, offering greater flexibility for fluid dynamics optimization. -
Extreme manufacturing efficiency: delivery time reduced to 1–2 days
Compared to traditional metal molds that cost tens of thousands and take several weeks, FDM printing drastically reduces cost and lead time, making it ideal for small-batch, multi-spec customization.
Application Case: Radiator Cooling Hose Mold – A One-Piece Efficiency Revolution
Project Background
An automotive R&D team urgently needed to develop an engine hose for a radiator cooling system. The structure was highly complex, with multiple spatial curves and irregular surfaces. Traditional CNC processing required part segmentation and assembly, failing to meet one-piece forming requirements or delivery within one week.
Rubber Hose Mold CAD Design
Solution
Using the INTAMSYS FUNMAT PRO 610HT and PEI1010 material, the mold was 3D printed.
-
Print size: 250 × 99 × 94 mm
-
Print duration: 25.7 hours
Results
-
56% cost reduction, 80% efficiency improvement
-
Dimensional deviation stabilized within ±0.1 mm, fully meeting assembly precision needs
-
Design freedom unlocked, dramatically shortening development and validation cycles
Finished Rubber Hose Mold
Test Verification
The mold underwent continuous high-temperature baking tests, demonstrating excellent dimensional stability. This verified the reliability of both the PEI1010 material under high heat and the consistent print quality of the INTAMSYS system.
Inner diameter before heating: 13.97 mm
Inner diameter after heating: 13.99 mm
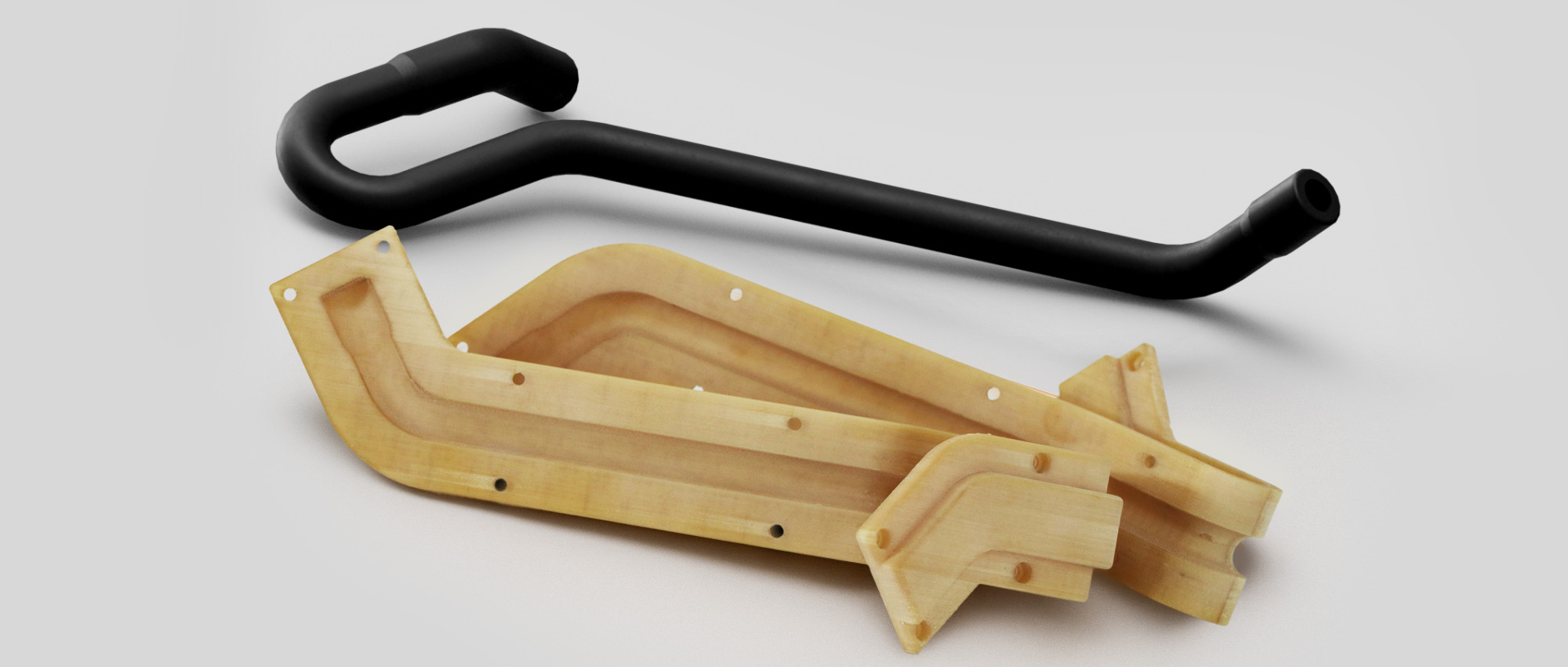
FDM 3D-Printed Rubber Hose Mold and Final Rubber Hose Product
Technology Empowerment Drives the Future of Flexible Manufacturing
With its precision, flexibility, and efficiency, the FUNMAT PRO 610HT + PEI1010 offers an ideal solution for automotive rubber hose mold manufacturing and unlocks broader applications in high-performance component production. It serves as a powerful engine for transitioning from traditional manufacturing to digital, green, and agile processes—and a solid foundation for the future of flexible manufacturing.
Stay connected with INTAMSYS as we continue to push the boundaries of additive manufacturing.
Comments